Innovationen für gezogene Kaltstauchqualitäten
Geschälter Draht und Sonderprofile außerhalb ziehtechnischer Standards und phosphatfreier Draht. Erfahren Sie mehr über unsere Innovationen für einen effizienteren Umformprozess von Kaltstauchgüten.
OPTI-S™: INNOVATIVE OBERFLÄCHENQUALITÄT BEI KALTSTAUCHGÜTEN
opti-S™ (Optimal Surface) von LÜLING setzt neue Maßstäbe in der Qualität von Oberflächen gezogener Kaltstauchqualitäten. Dieses Ausgangsmaterial ist insbesondere für hochwertige Bauteile von großer Bedeutung, die höchste Fehlerfreiheit für ihre Funktion gewährleisten müssen.
Mit opti-S™ können wir Ihnen eine nahezu perfekte Oberflächenqualität liefern, die die Weiterverarbeitung optimal unterstützt und neue Qualitätsstandards erfüllt. Ihr Vorteil: eine erhebliche Reduzierung kosten- und zeitaufwendiger Sortierprozesse nach den Umformprozessen.
Durch die enge Zusammenarbeit mit unseren Kunden und unter Berücksichtigung der späteren Anforderungen der Bauteile legen wir den Fertigungsablauf individuell fest. Dabei wird unter anderem ein Oberflächenabtrag durchgeführt. Der Einsatz von opti-S™ ist dabei unabhängig von der später erforderlichen Oberflächenbeschichtung des Drahtes möglich.
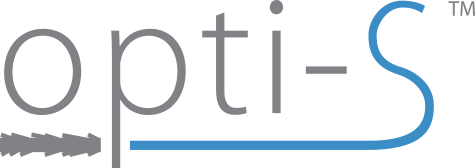
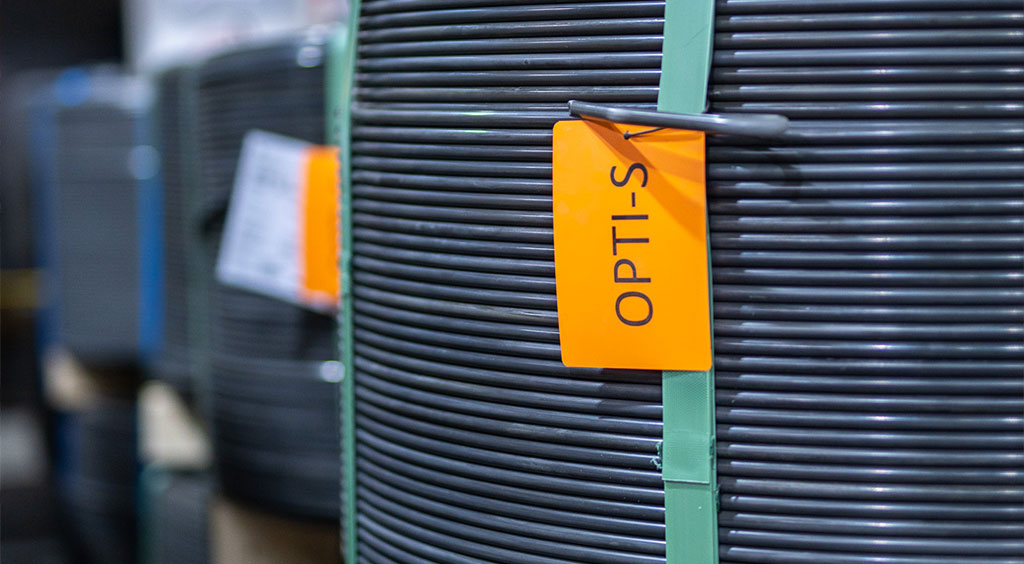
OPTI-S™: Herstellungsprozess
OPTI-S™: Anwendungen und Vorteile
Anwendung:
- Kaltstauchgüten im Ring oder Coil
- alle angebotenen Oberflächenbeschichtungen
- Abmessungsbereich: 6–25 mm
Vorteile
- reduziert kosten- und zeitaufwendige Sortierprozesse
- nahezu fehlerfreie Oberflächenausführung
- individuell auf spätere Bauteilerfordernisse abstimmbar
zero-P™: PHOSPHATFREIER DRAHT FÜR DIE KALTUMFORMUNG
Die Herstellung komplexer Kaltfließpressteile erforderte bislang hauptsächlich den Einsatz von Draht mit einer phosphatierten Oberfläche. Trotz einiger Fertigungsvorteile bringt dieser Ansatz auch Nachteile mit sich, darunter die kostspielige und umweltbelastende Entphosphatierung der Pressteile sowie die potentielle Gefahr einer Delta-Ferrit-Bildung bei thermischer Nachbehandlung, abhängig von Bauteiltyp und Festigkeitsklasse.
Diese Herausforderungen haben in der Kaltstauchindustrie zu dem langjährigen Bestreben geführt, Draht mit einer phosphatfreien Oberfläche als Ausgangsmaterial zu verwenden. Wir haben in enger Zusammenarbeit mit Kunden und Wissenschaftlern ein phosphatfreies Produkt entwickelt, das den hohen Anforderungen der Kaltmassivumformung entspricht.
Das einzigartige Know-how unseres Produkts zero-P™ (zero phosphate) basiert auf der Kombination von drei Schlüsselkomponenten, um eine Drahtoberfläche zu erzeugen, die die hervorragenden Umformeigenschaften unseres Materials bestmöglich unterstützt.:
- Ersetzen der herkömmlichen Phosphatschicht durch eine spezielle Beschichtung aus organischen und anorganischen Bestandteilen
- Eine im Verlauf des Prozesses optimierte Wärmebehandlung
- Einsatz spezieller Ziehsteintechnologien
Im Gegensatz zur Phosphatierung, bildet zero-P™ keine chemische Verbindung mit dem Grundmaterial, sodass es nach dem Umformprozess problemlos entfernt werden kann.
Vorteile von phosphatfreiem Draht
WEITERVERARBEITUNG
- keine chem. Verbindung mit dem Grundmaterial
- Verarbeitung auf Mehrstufenpresse ist technisch darstellbar
- komplexe Umformgrade realisierbar
- keine Bildung von Delta-Ferrit im Wärmebehandlungsprozess
UMWELTSCHUTZ
- reduzierte Pressölverschmutzung
- keine umweltbelastenden Phosphatreste
- keine kostenintensive und deklarationspflichtige Entsorgung
- keine Nitrate oder Schwermetalle in Abwässern
Aufwand & Kosten
- keine Kosten für den Entphosphatierungsprozess
- kein Zeitaufwand durch Reinigung der Phosphatrückstände
- verlängerte Lebensdauer der Werkzeuge und Hilfsmaterialien
pro-F™: Sonderprofile
Das LÜLING-Produkt pro-F™ (pro forming) ermöglicht die Herstellung von Sonderprofilen im Ring jenseits herkömmlicher ziehtechnischer Standards ermöglicht.
Mit geometrischen Anpassungen, die näher am Endprodukt liegen, lassen sich Umformstufen in Ihrem Fertigungsprozess einsparen. Darüber hinaus kann das Umformpotential, durch eine Vorverlagerung der ersten Prozessstufe in das Vorprodukt, erhöht werden.
Profitieren Sie von:
- optimierter Werkzeugkonstruktion
- Verbesserung der Präzision des Bauteils
- und der Reduzierung des Werkzeugverschleißes